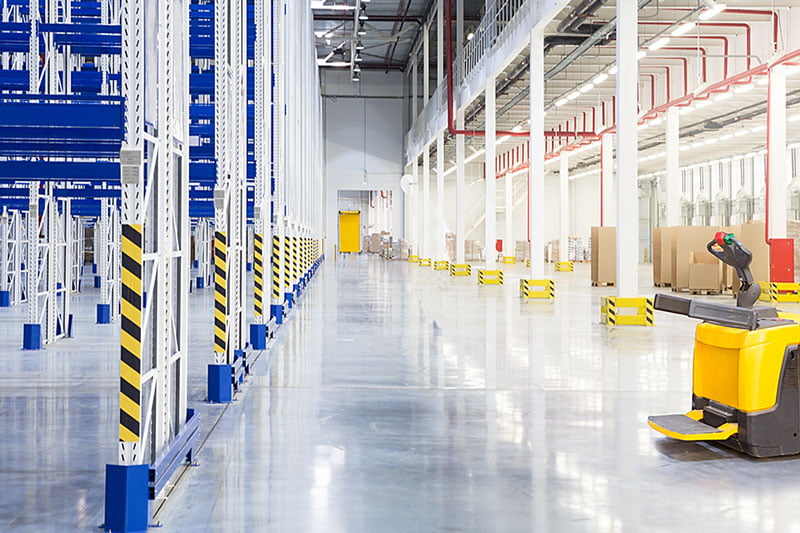
In a previous post we discussed the steps to take for designing-or redesigning-your distribution operations to support changes in order profiles. With your new design in place, the next step is implementation. The implementation phase is the longest and carries the most risk, mainly due to the large amount of capital invested and the complexity of dealing with many vendors and trades.
And, if the design is for a new facility, finding the right site or building can also be a timely and costly task. Whether you are customizing an existing facility or building new construction, below are the proper steps to take during each stage of the implementation phase:
Site and Vendor Selection
Once you have a document of the detailed design in hand, it is time to begin the selection process. During this step, you will:
- Find and secure a plot of land that accommodates the design, inbound and outbound access for trucks and enough space for employees' vehicles based on overall growth. If you are moving into a new area, this is a good time to get city, county or state incentives.
- Identify potential material handling equipment (MHE) providers and lead times. Depending on the MHE being used, you may have to execute these contracts immediately to ensure the equipment arrives on time.
- Develop an RFP to send to potential developers and builders. After evaluating all of your options, you will move into final negotiations with the selected partner.
Construction
After identifying and securing the site and vendors, the project moves into the construction phase. During this step, you will:
- Work with a construction manager to oversee site excavation, installation services, building construction and all other issues that arise along the way.
- Once the building is enclosed, you can begin receiving and staging the MHE. Make sure to prepare a detailed plan based on equipment arrival times and time to install to ensure this step goes smoothly. You may also need several project managers to oversee each type of system and equipment (most vendors will provide their own).
- Prior to moving into the testing phase, develop standard operating procedures based on how the equipment was designed to perform. These can be changed after testing is completed, but it is important to have a baseline document for comparison.
Testing
Once all of the equipment is installed, it is time to test the entire system. In an automated warehouse, this process can easily take a month (or longer for highly automated facilities) and typically consists of multiple tests, including:
- Unit testing specific equipment on its own
- Overall integrated testing between specific equipment and potentially different vendors
- Volume tests, including normal every day and stress testing
- Warehouse management system (WMS) testing with the warehouse control system (WCS) and/or warehouse execution system (WES)
Inventory
After all of the testing is completed, it is time to start bringing the actual inventory into the facility. This step requires a plan that allows the facility to gradually open to account for any issues that may occur and also outlines:
- What inventory should be brought in
- The timeframe for bringing in the inventory
- How much time you have before the building has to go live
Contact us today to learn how we can help you successfully start up your new distribution and fulfillment operations.
How can we help improve your supply chain operations?
Schedule a consultation or contact Tompkins Solutions for more information.
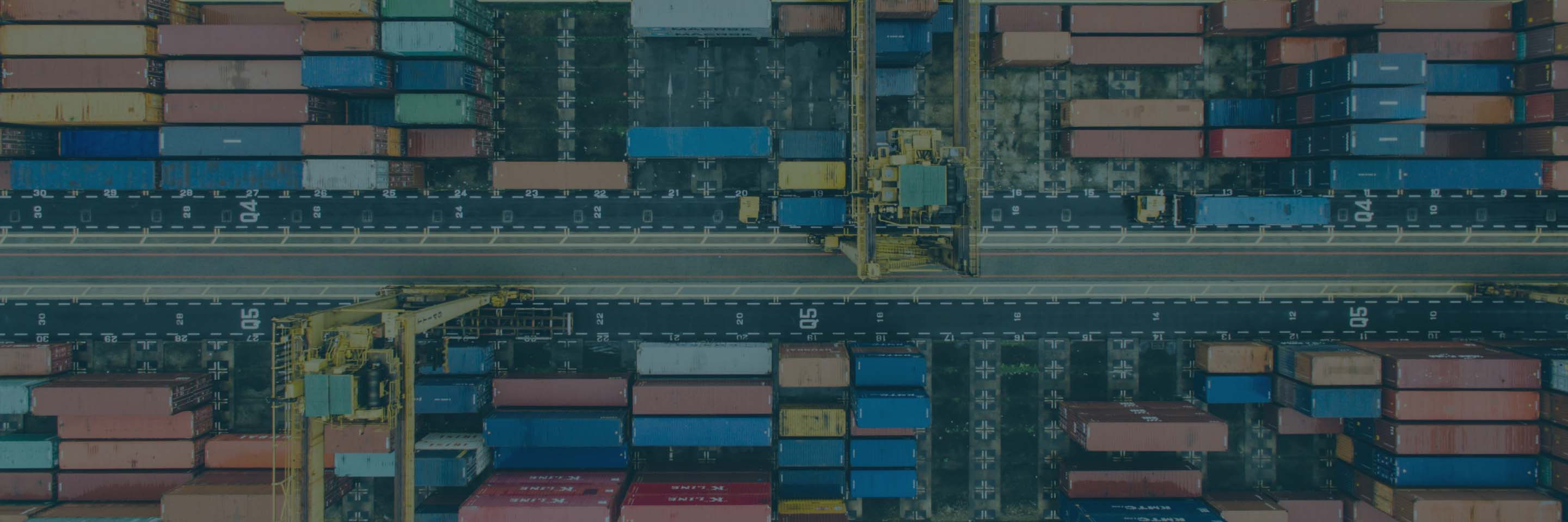
Featured Posts
Discover valuable resources to enhance your knowledge.